The research group for mechanical engineering and materials technology has broad expertise in the design of mechanical components, testing and development of materials, manufacturing methods and methods for load calculations and fluid dynamics.
Fatigue and structural integrity
The reason of the 98% of the failures of mechanical systems and the 60% of the failures of structures subjected to variable loading conditions is fatigue.
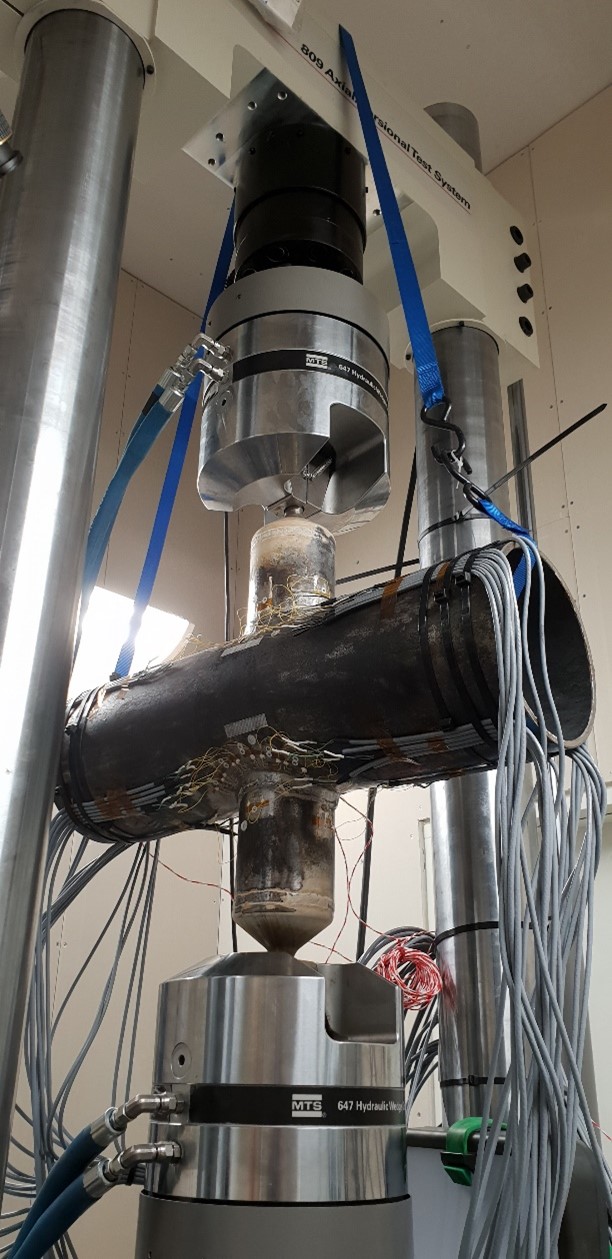
A main field of research and teaching activities of the department of Mechanical and Structural Engineering and Materials Science (IMBM) is the design of offshore structures, machine components, subsea systems, buildings and bridges etc. Fatigue damage accumulation modeling and life-time prediction of engineering structures under service loading are main research areas of the FSIG-UiS group. The research portfolio of our experts contains a significant number of publications, research monographs, editorial and review service for high-impact international journals, participation in research projects and collaboration with important industries. Furthermore, their results have international recognition by independent researchers from the academy and industry. Currently, the research team is working on improvement of methods and models for structural design, life-time prediction and health monitoring of structures and machine parts. The FSIG-UiS has access in modern facilities.
Material technology
In general, material technology is to understand the connection between microstructure, the internal structure of materials, and their properties.
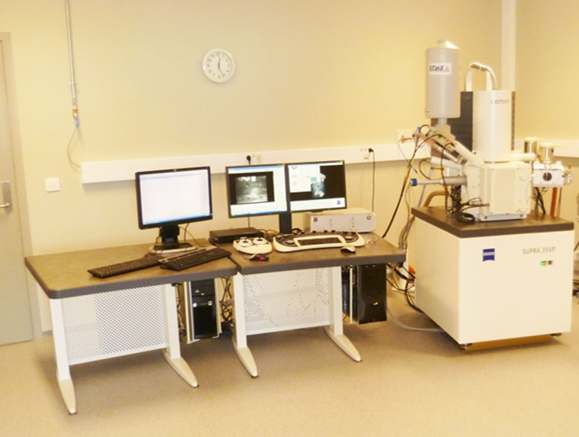
In connection with the green transition, the functional properties are of great importance. This may, for example, be how different microstructure affects the efficiency of solar cells or batteries. Our activity has mainly been aimed at metallic construction materials for offshore use related to how different microstructure affects the technological properties such as strength and corrosion properties.
Printing of metallic materials has been under great development in recent years. This method of production provides new opportunities that the industry finds interesting, but also new material technology challenges. Material produced by 3D printing has a far more complicated microstructure than the equivalent conventionally produced material. The complicated microstructure gives altered technological properties, often undesirable. The reduced properties in relation to the metal's potential opens up exciting material technology challenges where knowledge of the microstructure is crucial for making knowledge-based changes to the alloy composition and the printing parameters. These are exciting material technology challenges to take part in! The potential for the use of 3D-printed metal is significant if the technological properties are satisfactory. The companies can save money by, among other things, avoiding having large reserve stocks. This contributes to the green transition in that smaller metal must be produced; a small part is not made by removing a lot of metal from a large block as before. The need for large parts warehouses is reduced, as parts can be printed close to where they are to be used, when they are to be used. The CO2 footprint is reduced by requiring less metal to be produced and the need for transport is reduced by printing rather than traditional manufacturing.
Welding and in-service inspection
Our welding research is mainly focused on life extension of existing welds by estimation of welding induced residual stress profile in repair/critical welded joints.

Our research includes:
- Weld modelling of multi-pass weld joints (e.g., TKY) and estimation of welding induced residual stresses and distortions by use of custom based plugins and thermo-mechanical analysis respectively in simulation environment like ABAQUS.
- Welding procedure qualification record (WPQR) of critical weld as per fabrication codes like EN 15614-1, NORSOK M-101.
- Non-destructive testing (NDT) for defect assessment of weld by use of techniques like Magnetic particle inspection (MPI), dye penetrant testing (DPT), ultrasonic testing (UT) and phased array ultrasonic testing (PAUT).
Design and Manufacturing
The manufacturing sector is considered as backbone of the economy of many countries.
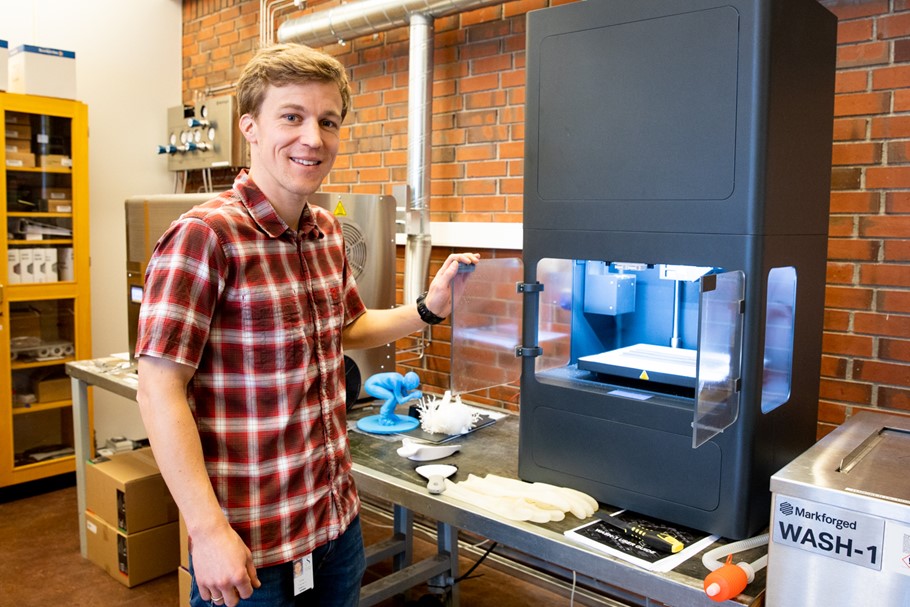
Understanding that the next generation advanced manufacturing requires enabling technologies such as additive manufacturing, artificial intelligence (AI), robotics and automation, among others, current research in advanced manufacturing at IMBM mainly focuses on Additive Manufacturing (AM). Within this technology, our research activities are divided into three:
- application areas of AM such as renewables and medical sectors
- design for additive manufacturing (DfAM), including modelling and simulation
- materials and processes including parameters that optimize performances
The next generation advanced manufacturing further demands that the process realizes digitalization, environmental sustainability, and more flexibility for customized production of products. AM based process can address these demands, though there are still challenges related with the competitiveness of the process in terms of economic sustainability and material compatibility. The research team in AM research at UiS work with relevant regional and national sectors to bring the AM technology as a mature and feasible manufacturing method in key strategic areas.
More information here: Lean 6σ Learning Academy | University of Stavanger (uis.no)
Fluid dynamics and CFD
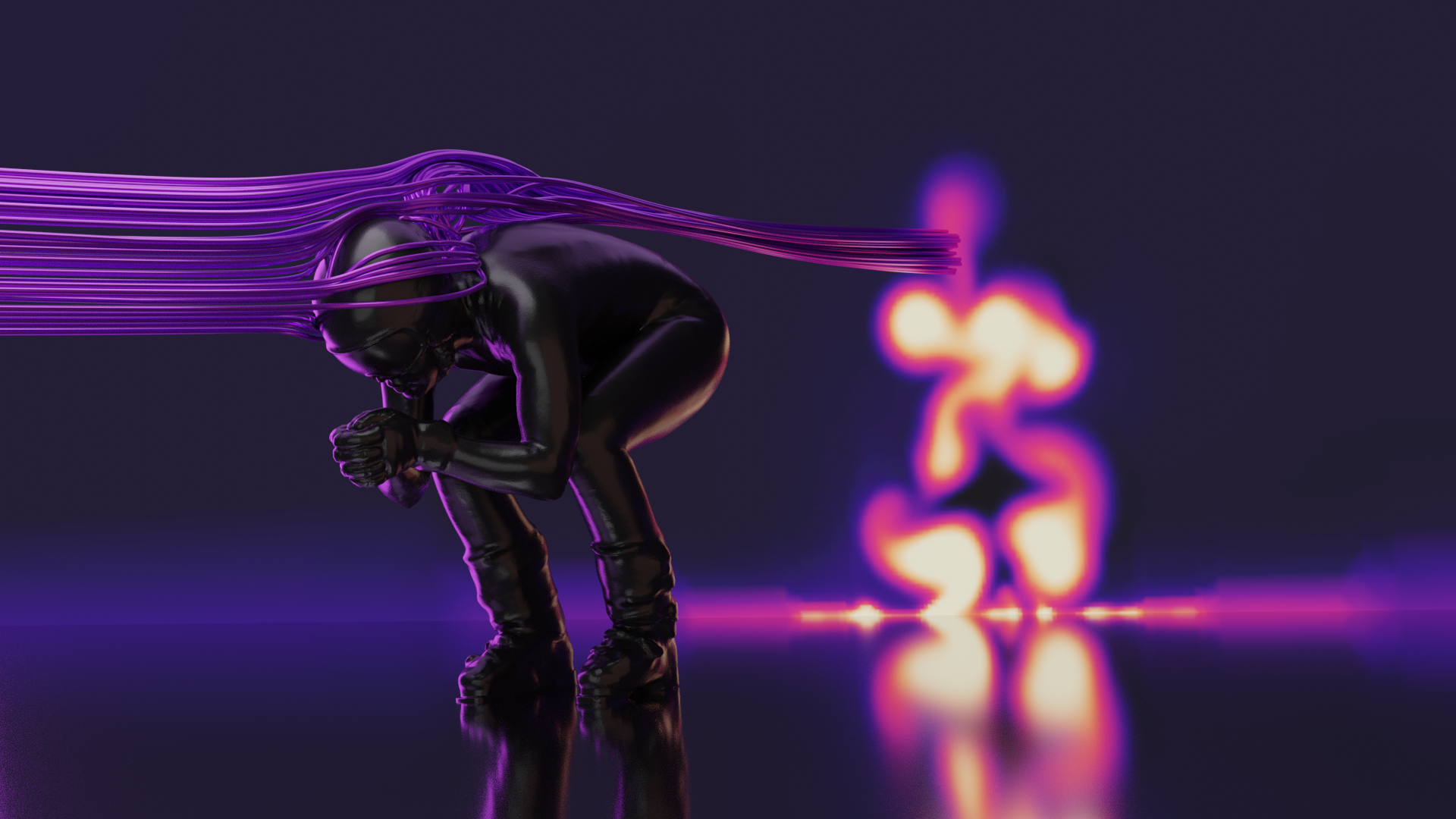
Our research in fluid dynamics spans several areas.
- Aero- and hydrodynamics: We explore how we can design more efficient rotors for drones and more efficient blades for wind turbines and tidal turbines.
- Sports aerodynamics: We develop detailed simulation models that can be used to reduce air resistance for use in sports and other industries.
- Wind flow in urban areas: We develop effective simulation tools to study how new buildings affect wind conditions in urban areas.
- Multiphase flow: Using detailed simulation models, we can provide insight into complex processes such as well construction and other processes in the oil and gas industry.
- Medical technology: We are researching how to create patient-specific models of blood flow to streamline surgical procedures.
Researchers
The ball that makes you want to move
What happens when a business economist and a concert violinist team up? The answer is Muzziball – a human-centric innova...
Enhancing efficiency and sustainability in Lean Management
Daria Larsson defended her PhD thesis at University of Stavanger 11 April 2025.
Numerical modeling of monopile foundation removal process for offshore wind turbines
Soheil Salahshour Langeroodi conducted research on numerical modeling and analysis of offshore monopile foundation remov...
Research on urban wind and pedestrian wind comfort
Trond-Ola Hågbø defended his PhD thesis with the title “Towards Realistic and Efficient Computational Fluid Dynamics Sim...
Successful completion for PhDs at UiS' partner university
Together with Wallaga University in Ethiopia, UiS is part of the education project INDMEET (Institutional Network for De...
Design, Modelling and Analysis of Combined Wind and Wave Energy Systems for Intermediate Water Depths
Chern Fong Lee has conducted research on the numerical modelling of Combined Wind and Wave Energy Systems for Intermedia...
Celebrating PhD achievements in circular economy and supply chain innovation
Noorhan Firdaus Pambudi and Kartika Nur Alfina have successfully completed their doctoral projects in the Department of ...
Yara's Birkeland Prize 2024 to Song Lu
Yara’s Birkeland Prize for 2024 in chemistry was given to doctor Song Lu for his thesis titled “Transition-metal-mediate...
Design optimisation for floating offshore wind turbines
Anja Schnepf defended her PhD-thesis titled "Design optimisation of Power Cable Configurations for Floating Offshore Win...
He has 3D printed a training model for spinal anesthesia
Øyvind Time's master's thesis can help make everyday life easier for healthcare personnel who must learn how to take a f...
Numerical modelling of floating docks
Jianan Zhang has performed research on the numerical modelling of the floating docks. On 31 May, she defended her doctor...
Successful UiS Aerospace rocket launch
The UiS Aerospace rocket launch took place successfully 27 April in Helleland.
Design of autonomous underwater vehicles
Yucong Ma has researched dynamic analysis and design of subsea shuttle tanker systems.
Receives award for innovation in computing
Professor Dimitrios G. Pavlou was recently awarded the prestigious Hojjat Adeli Award for Innovation in Computing.
Their article in Physics of Fluids was selected as “Featured Article”
Physics of Fluids (PoF) belongs to American Institute of Physics (AIP) academic journals and is traditionally known as o...
UiS researchers were awarded with scholarship
Only 34 young researchers around the world were selected to participate in the OMAE2023 Outreach for Engineers Forum. Th...
Large Offshore Wind Turbines: Structural design accounting for non-neutral wind conditions
How to reduce cost of energy for future large offshore wind turbines in free-wind and wake conditions by using full-scal...
Olympiad in Engineering Science summed up
Scientists and engineers from all over the world were gathered in Olympia in Greece to take part in the first ever engin...
UiS takes part in research on Arctic shipping
The goal is to find environmentally friendly solutions for shipping and transport in Arctic waters.